Inleiding
Tweakers.net had eerder deze maand de mogelijkheid om een kijkje te nemen bij de Dane-Elec geheugenfabriek in Galway, Ierland. Deze kans hebben we uiteraard niet links laten liggen, en zo kwam het dat Femme en Wouter eerder deze maand een dag hebben rondgekeken op de plaats waar al het geheugen van Dane-Elec voor de Europese markt vandaan komt, om uiteindelijk een review te kunnen schrijven over dit proces.
Voor we ingaan op het produceren van geheugen eerst wat uitleg over de organisatie achter Dane-Elec. Het bedrijf is in 1985 opgericht door de Fransen David Haccoun en Nessim Bodokh, die elkaar twee jaar eerder leerden kennen omdat ze samen op dezelfde afdeling werkten. De twee companen besloten voor zichzelf te beginnen, en startten een eigen bedrijf in alarmsystemen en doorsluizen van allerlei verschillende soorten elektronische componenten. Na twee jaar de markt verkennen en ervaring opdoen besloten de twee ondernemers om zich te specialiseren in de distributie van geheugen voor computers.
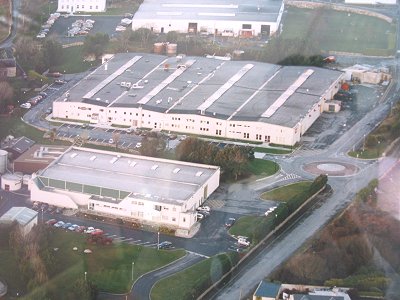
Luchtfoto van Dane-Elec in Galway
Omdat voor het maken van geheugen grote investeringen en knowhow nodig zijn bleef het de eerste jaren bij doorverkopen van producten van derden. Al redelijk snel werd Dane-Elec een grote Europese distributeur van het Japanse merk Oki, maar ook Samsung en Siemens repen werden doorverkocht aan groothandels. De ambitie was echter groter; men wil zelf geheugen kunnen maken. In 1996 wordt daarom een fabriek geopend in het Ierse Galway. Twee jaar later volgt een tweede faciliteit in Irvine, Californië. Deze is echter een stuk kleiner dan het gebouw in Galway.
Dane-Elec wordt nog steeds geleid door David (CEO) en Nessim (COO), vanuit het hoofdkantoor in Frankrijk. Naast het bestuur en een deel van de verkoop wordt er op de Franse lokatie ook aan research en development gedaan. Het bedrijf heeft contacten opgebouwd met alle grote spelers in de geheugenmarkt en is in 1997 naar de beurs gegaan. Vanwege het succes van de producten zijn er inmiddels kantoren geopend in Nederland (Capelle aan de IJssel), België, Duitsland en Engeland, om de verkoop, service en contacten met klanten zo goed mogelijk te kunnen onderhouden. Vanuit de Ierse productielijnen wordt al het geheugen aan de Europese verkopers geleverd. De Amerikaanse afdeling van Dane-Elec is wat dat betreft zelfstandig; in Californië wordt de complete productie voor het Amerikaanse continent gedraaid, en er is ook een eigen verkoopdivisie aanwezig.
De fabriek
De Ierse fabriek staat zoals gezegd nabij Galway, een stad met ongeveer 70.000 inwoners in het westen van het land. Er werken ongeveer 140 mensen in drie ploegen om de vijf productielijnen - verdeeld over een grote hal met een oppervlakte van zo'n 2300 vierkante meter - vierentwintig uur per dag en zeven dagen in de week werkend te kunnen houden. Als het nodig is lukt het dit team om ongeveer 20.000 repen geheugen per dag te bouwen. Vroeger was dit soort capaciteit hard nodig, en was er zelfs een tijd sprake van een grote uitbreiding. De markt is tegenwoordig echter een stuk minder goed, waardoor de fabriek alleen rond Kerstmis op volle toeren draait.
Wie denkt dat er in zo'n grote fabriek aan massaproductie wordt gedaan en de bestellingen gewoon uit een groot magazijn worden gevist heeft het mis. Er kunnen namelijk tientallen verschillende soorten modules besteld worden. De software van de machine's kan in een handomdraai worden aangepast om gebruik te maken van andere printplaten of onderdelen. Er zijn honderden van deze programma's gemaakt voor allerlei verschillende geheugens en componenten - van EDO-SIMM tot RDRAM. Deze laatstgenoemde soort geheugen wordt overigens niet gemaakt in Galway. De testapparatuur voor Rambus geheugen is namelijk erg prijzig om aan te kopen, en omdat er relatief weinig vraag naar RIMM's is heeft men besloten om dit geheugen gewoon elders in te kopen en verder te distribueren. Ook diverse andere producten, zoals de cardreaders en SmartMedia kaarten, worden niet in eigen keuken gebouwd.
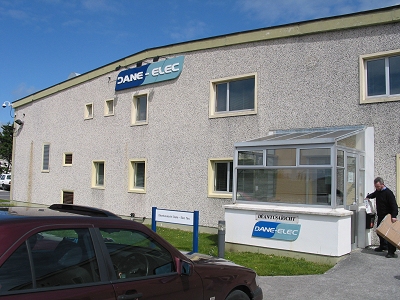
Naast het omvangrijke assortiment en de beveiliging van het magazijn is er nog een ander belangrijk argument om niet te werken met grote voorraden geheugen, en dat zijn de financiën. De prijzen in de geheugenmarkt zijn zoals iedereen wel weet sterk onderhevig aan schommelingen. Om de schade daarvan enigszins te beperken wordt er ook on-spot ingekocht. Verschillende bedrijven - waaronder Toshiba, Samsung en Infineon - slaan hun chips op in een grote dikke kluis binnen de fabriek van Dane-Elec. Hoewel het geheugen op dat moment klaar ligt om gebruikt te worden, blijft het formeel nog steeds eigendom van de leverancier. Zodra er bij Dane-Elec een order binnenkomt voor modules en de chips uit de kluis worden gehaald worden de chips officiëel gekocht, voor de op moment geldende prijs. Het voordeel hiervan is dat de prijzen van de modules direct kunnen meeprofiteren van een verlaging van de prijzen van chips.
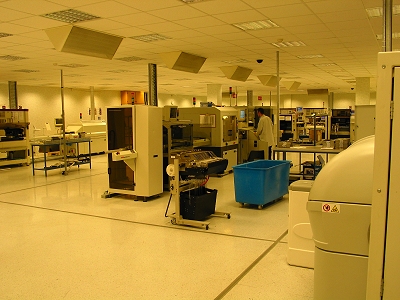
Een indruk van de productiehal
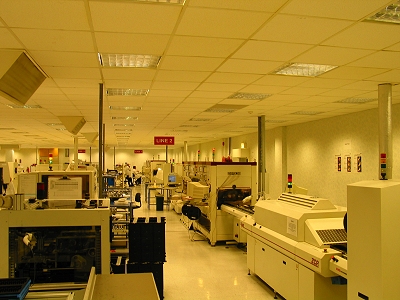
Productielijn nummero 2
Dane-Elec is nog niet zo groot dat ze zelf chips maken, en men heeft dus ook geen echte cleanroom zoals Intel en AMD gebruiken om waferscanners in te plaatsen. Toch probeert men de productieruimte zo goed mogelijk schoon en stofvrij te houden, om te voorkomen dat een verdwaald stofdeeltje een DIMM kapot maakt door een slecht contact te veroorzaken. Ook moet er in de fabriek opgepast worden voor statische elektriciteit; op ieder bureau liggen anti-statische matten en iedereen die binnen rondloopt moet een speciale jas aan en een band om z'n voet doen om zich te aarden.
Printplaten voorbereiden
Hoe de orders in Galway verwerkt worden zal op deze en de volgende pagina's beschreven worden aan de hand van textuele uitleg en foto's. Helaas mochten we onze digitale camera's niet zomaar overal op richten, omdat een deel van de gebruikte apparatuur het label top-secret draagt. Het komt in deze industrie jammer genoeg voor dat concurrenten zich voordoen als verkoper, potentiële klant of journalist, om zo te achterhalen wat voor testapparatuur Dane-Elec gebruikt, of hoe ze het voor elkaar krijgen om CompactFlash kaartjes zo snel in elkaar te zetten. Alle plaatjes die we mee de fabriek uit wilden nemen moesten dan ook gescreend worden door het hoofd van productie.

Werd Femme omgekocht door de Russen?
Terug naar de bestellingen. Een order bestaat uit vijf tot tweeduizend modules, dit kunnen verschillende types geheugen zijn. Grotere opdrachten worden verdeeld over meerdere werkorders van tweeduizend eenheden per stuk. De eerste stap van het uitvoeren van een order is het verzamelen van de verschillende onderdelen uit het magazijn. Denk hierbij aan zaken zoals printplaten, chips en weerstanden.
De printplaten worden per vijftig stuks in een feeder gestopt, die ze doorstuurt naar de screen printer. Deze gebruikt een zeer nauwkeurig pompmechanisme, gestuurd door een speciale camera, om soldeerpasta in het juiste patroon op de printplaat te stempelen. Dat moet gebeuren vóór de onderdelen geplaatst worden, want er wordt al eeuwen niet meer gebruik gemaakt van PCB's met gaten die aan de onderkant gesoldeerd kunnen worden. De pasta in ruwe vorm is een zeer giftige grijze massa, maar is vooral ook erg duur omdat er onder andere zilver zit verwerkt. Dit is niet alleen bevorderlijk voor het uiterlijk van het eindproduct, maar ook voor de geleiding.
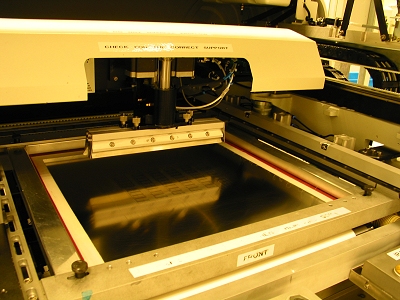
De screen printer - in de weerspiegeling is zichtbaar waar de printjes horen te liggen
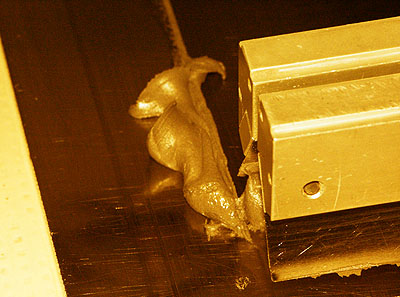
Restjes soldeerprut

Hier komen de wannabe-modules de printer uitgerold
Via een lopende band gaan de printplaten verder naar een Philips Sapphire machine. Deze kan in minder dan een seconde een klein component op zes modules tegelijk aanbrengen. De robotarm die deze taak verricht pakt de onderdelen op van speciale rollen die hem gevoed moeten worden, en kan 24 verschillende soorten klein grut tegelijk vasthouden. De computer van de Sapphire die de arm aanstuurt vertrouwt op informatie van een high-res 10x zoom camera om de onderdelen op de juiste plaats te zetten.
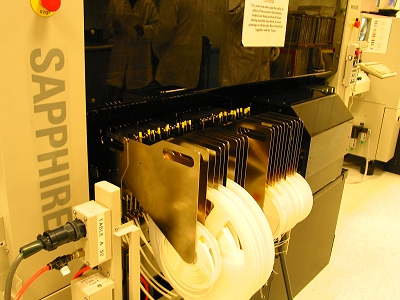
Sapphire in al zijn l33t-heid
De ingewanden van het apparaat
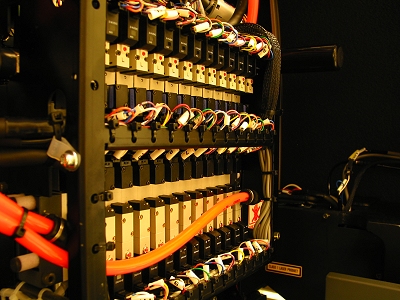
De bewegende arm met 24 koppen
Eén van de gevoelige camera's
Aanvoer van onderdelen
Het mechanisme dat de weerstandjes van de rol naar de machine brengt
Aan rollen geen tekort bij Dane-Elec
Aanbrengen van geheugenchips
De op de vorige pagina beschreven Sapphire machine kon alleen kleine onderdelen op de printplaat zetten, dus voor het grote werk moet de hulp van een ander apparaat worden ingeroepen; de Topaz. Dit is net als de Sapphire ook een product van Philips, dat qua globale opbouw zeer veel overeenkomsten vertoont. Het verschil is dat de Topaz dankzij een slim systeem dat on-the-fly vision alignment wordt genoemd met onderdelen tot 32 millimeter (lees: geheugenchips) kan omgaan. De machine kan met deze beweegbare camera's in principe ook kleinere onderdelen plaatsen, maar dat wordt zo veel mogelijk aan de Sapphire overgelaten. Deze haalt namelijk grofweg 24.500 plaatsingen per uur, terwijl de Topaz er 'maar' iets meer dan 14.000 doet in dezelfde tijd.
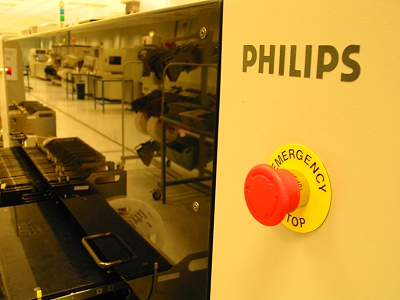
Alle apparatuur wordt glimmend schoon gehouden
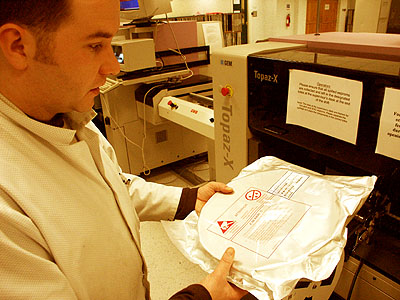
De geheugenchips komen net als de weerstandjes binnen op grote rollen

...en zitten ook nog eens individueel verpakt

Voor iedere soort module moet een apart programma geladen worden
Als alles op z'n plaats zit is het moment van het bakken eindelijk aangebroken, de chips gaan naar de oven, of zoals Dane-Elec het apparaat noemt: computerized thermal processing system. De bedoeling van het apparaat is om de pasta op de PCB voor een deel te verdampen, voor een deel te smelten en voor een deel weer hard te laten worden, zodat alle geplaatste onderdelen netjes op hun plaats vast komen te zitten. Hiervoor zijn temperaturen nodig die behoorlijk hoog op kunnen lopen. Overklokkers weten dat een processor die de 100 graden bereikt bar weinig overlevingskans heeft, maar de geheugenchips moeten in de oven bijna drie keer zo hoge temperaturen doorstaan.
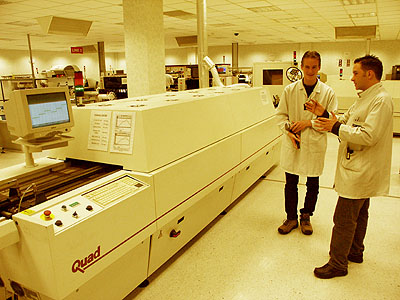
Overzichtshot van de oven
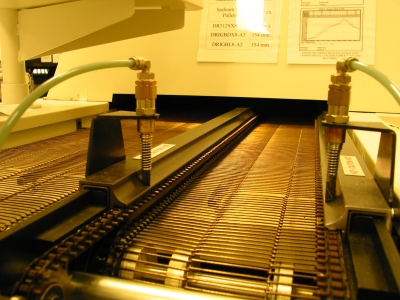
Om de volle breedte van de oven te benutten kan de computer de aanvoerband verplaatsen
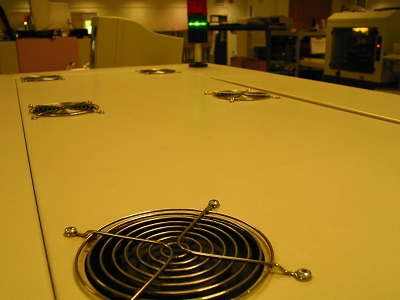
Fingerguards, maar waarschijnlijk geen standaard 80x80 fans
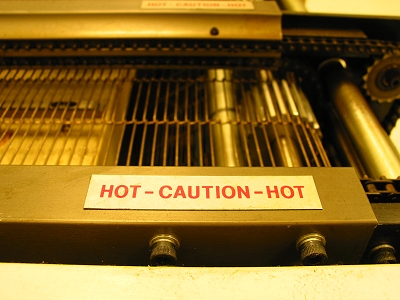
Voor mensen die niet snappen dat spullen in een oven heet worden
De fabrikant van de geheugenchips stelt in samenwerking met de leverancier van de soldeerpasta een model op voor de oven waarmee gesoldeerd kan worden zonder dat de chips het begeven. De chips kunnen twee keer een tocht op de lopende band door de oven overleven, met zone's waarin de temperatuur kan oplopen tot 270 graden celcius. De reden dat ze het twee keer moeten kunnen doorstaan is dat double sided geheugen twee keer door de productielijn heen moet.
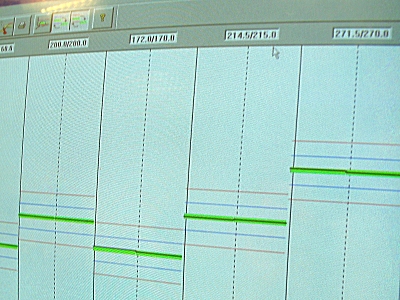
Voorbeeld temperatuurconfiguratie van de oven
Als de modules uit de oven komen worden ze in een feeder aan de andere kant van de productielijn geplaatst. Door middel van lampen wordt aangegeven of er nog plaats vrij is of dat het tijd is om het ding te legen. De printplaat legt van de feeder in het begin tot de feeder aan het einde ongeveer 20 meter af, en worden meteen zodra ze klaar zijn gesteriliseerd en voorzien van een label.
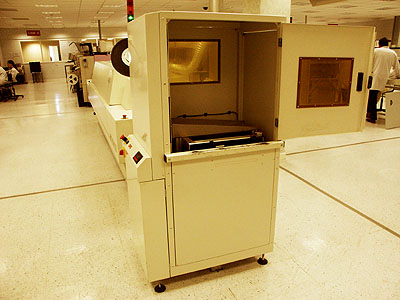
Eindstation
CompactFlash
Hoewel het grootste deel van de fabriek is ingericht voor SDRAM en DDR geheugen, begint de vraag naar CompactFlash ook steeds grotere proporties aan te nemen. Vooral Nederland vertoond een grote groei op dat gebied. Wij Nederlanders zijn "a pain in the ass" aldus de medewerkers van de fabriek
, omdat we speciale retaildoosjes willen, terwijl winkels in andere landen dat niet nodig vinden of zelf doen.
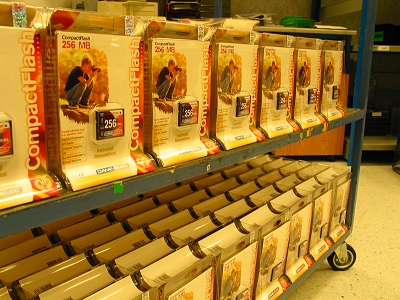
Lading met 256MB CompactFlash kaartjes in nette doosjes voor de Nederlandse markt
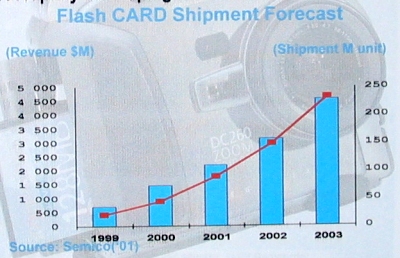
Verwachte groei wereldmarkt voor flashkaarten
De basis van het maken van CompactFlash verschilt niet veel van de methode die voor repen geheugen gebruikt wordt. De printplaat biedt plaats aan vijf geheugenchips en een controller. De reden dat de controller op de kaart zit en niet in het apparaat dat gebruik wil maken van het geheugen is dat ondersteuning voor snellere of grotere chips makkelijk te realiseren is.
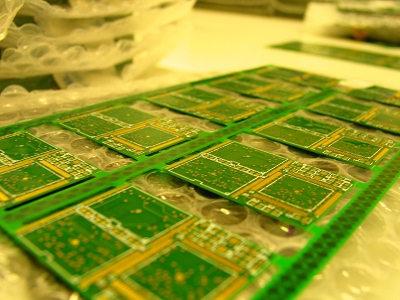
CompactFlash printplaten
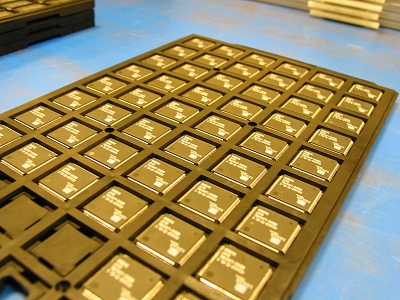
Chips voor op de CompactFlash printplaat
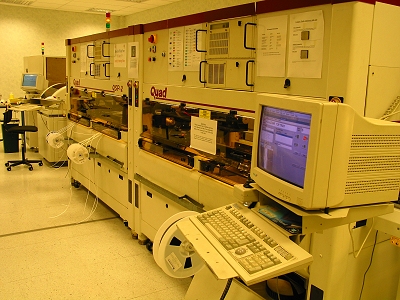
CompactFlash-in-elkaar-zet-machine
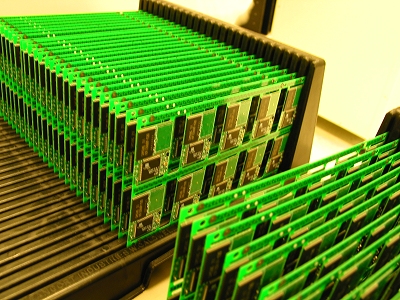
Genoeg ruimte voor een paar vakantiekiekjes
Als de printplaat eenmaal klaar is moet deze nog in de welbekende behuizing worden geplaatst. Deze wordt geleverd als twee losse helften die met behulp van ultrasone trillingen aan elkaar gesmolten worden. Andere fabrikanten gebruiken een systeem waarbij de verpakking als een doosje dichtklapt. Na het inpakken zijn de kaarten klaar om getest te worden.
Helaas mochten we de kleine details waarmee Dane-Elec zich onderscheidt van de rest niet onthullen, maar we kunnen er vanuit gaan dat ieder bedrijf zo z'n eigen geheimen heeft.
Bepaalt marktleider zijn ze niet, goeie naäpers wel, dus zo spannend zullen voor de grotere die geheimpjes wel niet zijn toch?
Voor de jongere bedrijven kan het misschien nog wel intressant zijn. Noujah, elke voordeeltje is er 1 dat telt als't slecht gaat zeker
Wat'k wel mis in dit artikel is waarop en hoe de onderdelen geselecteert en geverifiëerd worden.